In New South Wales, testing and tagging requirements are guided by specific legislation to protect workers and ensure safety on construction sites.
Testing and Tagging Legislation in NSW
The primary legislation governing testing and tagging in NSW is the Work Health and Safety Act 2011 and the Work Health and Safety Regulation 2017.
These regulations stipulate the need for regular inspection, testing, and tagging of electrical equipment used in construction to minimise risk to workers.
According to the WHS Regulation, any electrical equipment on a construction site must be regularly inspected and tested by a competent person to ensure it is safe to use. You can engage a reliable testing and tagging service in Sydney to meet these regulatory requirements and ensure compliance.
Enforcement of these regulations is carried out by SafeWork NSW, the regulatory body responsible for workplace safety, which conducts audits and inspections to ensure compliance.
How often is testing and tagging required?
Testing and tagging intervals are guided by AS/NZS 3760 for the construction industry.
For construction sites, testing is generally required every three months for portable RCDs, tools, and other electrical equipment. This frequency addresses the higher risk of wear and damage due to the demanding nature of construction environments.
Additionally, tools used in lower-risk areas, such as offices, may be tested less frequently, typically every 6 to 12 months. New equipment does not require testing upon initial entry into service, but must undergo testing once it is in use depending on its purpose.
Types of Electrical Equipment That Require Testing and Tagging in Construction
Electrical equipment used on construction sites is exposed to harsh conditions, which increases the risk of wear and potential faults. Specific equipment types must undergo regular testing and tagging to ensure safety. These include:
Power tools and other portable appliances
Corded power tools such as drills, saws, and grinders, as well as other handheld or portable appliances, are commonly used on construction sites. Only corded tools and appliances require testing and tagging, while battery-operated tools are exempt. However, chargers for battery-operated tools still require testing to ensure safe operation.
Three phase devices
Heavy-duty equipment powered by a three-phase supply, like welders, compressors, and large machinery, requires more rigorous testing. The process involves checking for insulation resistance, earth continuity, and functional controls due to the higher electrical load, which poses a greater risk of hazards.
Portable RCDs
RCDs are critical safety devices that disconnect power if a fault is detected, preventing electric shock. On construction sites, RCDs must be tested every three months to verify functionality. Testing typically includes a push-button test and a more thorough technical check to confirm the device’s effectiveness in mitigating electrical risks.
What information is required on tags?
Tags must display key information, including:
- Date of the test
- The next due date for testing
- Tester’s name or license number
- Test outcome (pass or fail)
Colour Coding
A colour coding system is used on construction sites to identify when equipment was last tested:
- Red for January to March
- Green for April to June
- Blue for July to September
- Yellow for October to December
The colour-coded tags make it easier for workers and inspectors to identify out-of-date equipment and enhance compliance with safety regulations.
Record Keeping and Documentation
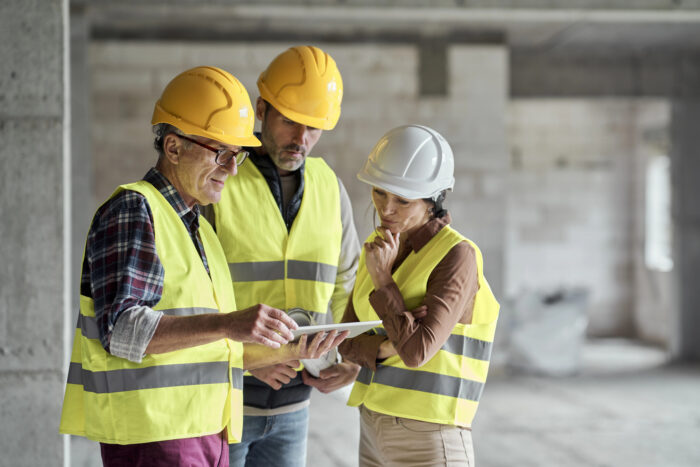
Detailed record keeping and documentation are essential to the testing and tagging process, ensuring ongoing compliance with safety regulations and facilitating effective safety management. The following elements should be included in these records:
Equipment Details
Each record should identify the specific equipment tested, including details such as the equipment type, make, model, and serial number. This ensures that each item can be tracked individually and its test history reviewed.
Test Results
Documentation must include the results of each test conducted. This should indicate whether the equipment passed or failed the inspection, along with any measurements or readings taken during the test (e.g., insulation resistance, earth continuity).
Corrective Actions
Records should detail any corrective actions taken for equipment that failed the test. This includes information on repairs made, replacements of parts, or the removal of the equipment from service. It should also note the date and outcome of any follow-up tests to ensure the issues have been resolved.
Tester Information
The name and qualifications of the person who performed the testing should be recorded. This verifies that the testing was conducted by a competent individual.
Testing Dates
It is important to record the date of each test and the next scheduled testing date. This helps ensure that testing is conducted at the required intervals and that all equipment remains compliant with safety standards.
Hire a Testing and Tagging Company that understands the Construction Industry
Testing and tagging devices on construction sites are essential in NSW, helping to minimise electrical risks on worksites.
Adhering to the WHS Act and Regulations, employing a reliable testing and tagging service in NSW, and maintaining detailed records are essential to ensure compliance.
At Precision Test and Tag, we can help you keep your equipment safe through regular testing and tagging at the required intervals. Contact us today for a quote.