Testing and tagging of electrical equipment is a vital procedure for most industries. It involves testing appliances with power cables to ensure they are safe in different workplace settings.
AS/NZS 3760:2022 outlines the electrical safety standards and safety inspections needed for industries. Naturally, some industries operate in harsher conditions and require more frequent electrical testing than others. Testing and tagging frequency often depend on the type of equipment, environment and regulations. The guide will dig deeper into the frequencies for each industry and how they affect you.
Industry guidelines for testing and tagging
While electrical appliance testing is compulsory in NSW, the frequency of testing and tagging depends on the industry you operate in. For example, the construction and mining industries have more frequent testing standards than others due to the nature of the work.
Construction, demolition and mining
The recommended intervals for testing and tagging in mining, construction, and demolition sites are every 3 months for portable equipment and flexible electrical cords such as extension leads. For fixed and transportable equipment, it is every 6 months. Portable equipment may include power tools such as drills, cutting machines, grinders and saws. A push button test is required before each use for portable RCDs while operating tests are required every 3 months. Any hired equipment must be tested when first introduced into service and then in accordance with appropriate intervals. These 3 industries must also follow the RGBY model for test and tag colours every 3 months.
Factories and workshops
For factories, workshops and manufacturing, testing and tagging of electrical equipment is required every 6 months. This includes Class 1 equipment, cord sets, extension sets and EPODs. Portable RCDs in these environments require daily or before-every-use push button tests. The frequency for operating time tests for portable RCDs is every 12 months.
Other high-risk environments
For environments where the equipment or supply flexible cord may flex when used in normal settings, is open to abuse, or is in a hostile environment, electrical equipment testing and tagging is required every 12 months. For RCD testing, the push button test for portable RCDs is every 3 months and every 6 months for fixed RCDs.
Hotels and accommodation-style properties
Testing and tagging of electrical equipment in hotels and accommodation-style properties are every 2 years. Push button tests for portable and fixed RCDs are every 6 months while the operating time test for portable and fixed RCDs is every 2 years.
Types of equipment that need to be tested
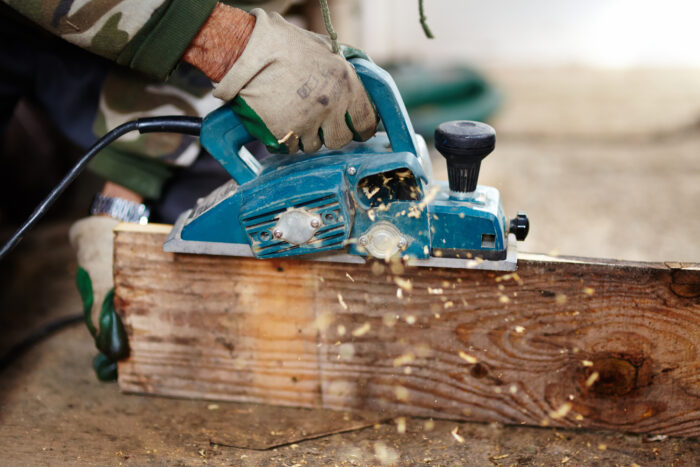
All fixed and portable electrical equipment and residual current devices (RCDs) can be tested. A wide range of electrical equipment will require testing and tagging to ensure safety, compliance and function. The cost of testing and tagging will depend on the frequency and number of appliances being tested.
- Appliances include devices such as computers, printers, toasters and microwaves for testing.
- Power tools with a power cable include grinders, drills, sanders and saws.
- Extension cords, electrical cords, power boards and adapters.
- Machinery including welding machines, generators and motors.
- Cables and wiring used in different applications.
- Fire extinguishers and other types of fire equipment – although fire extinguisher testing falls under a different Australian Standard, more specifically AS 1851.
- Emergency light testing under AS/NZS2293
Legal requirements for testing and tagging
In NSW, the legal requirements for testing and tagging electrical equipment are governed by the Work Health and Safety Regulation 2017. Businesses must ensure that all electrical equipment is safe and regularly inspected, tested, and maintained by a competent person.
This is particularly essential if electricity is supplied through an electrical outlet exposed to diverse operating conditions, including moisture, heat, vibration, mechanical damage, or corrosive substances. The frequency of these tests may vary based on the nature of the work environment and the type of equipment used.
The results of these inspections should be recorded and tagged. Any electrical equipment that doesn’t pass the inspection must be immediately disconnected or removed from service until it is repaired or replaced.
Testing and tagging also has several benefits. It helps identify faulty and damaged equipment before any major damage can occur, which keeps people and property safe. It also reduces the risk of breakdowns and downtime because faults are picked up beforehand, saving a business time and money to fix it.
Proper testing and tagging also ensures a trail of documentation showing that you have done your due diligence as a company. It also means you are well-prepared in case of any business or compliance audits, demonstrating that you have done everything possible to prevent electrical accidents in your workplace.
Who can test and tag in NSW?
In NSW, only competent persons can do testing on electrical equipment. They must have the appropriate training and qualifications to carry out the work safely and carefully. Testing must always be in accordance with AS/NZS 3760:2022, which outlines the requirements for testing, maintaining and storing electrical equipment in different workplace settings.
The main purpose is to ensure that all electrical equipment used in workplaces is safe and not harmful to people and property. Once the test is complete, a tag is attached to the appliance to indicate whether it has passed or failed and the due date of the next test based on the equipment class and industry. Tags must be clear and legible and indicate information such as testing company, date of test, appliance tested and due date of next test.
Consequences of improper testing and tagging
Equipment that hasn’t been properly tested and tagged might have hidden electrical faults or defects. This increases the risk of electrical shocks, fires, and other accidents that can cause injuries or fatalities.
Accidents resulting from faulty equipment can lead to property damage and medical expenses where people have been injured. In some instances, businesses may also incur legal expenses, which can financially burden business owners.
Testing and tagging play a crucial role in identifying equipment that doesn’t meet safety standards and can protect businesses from potential issues down the track. Failure to do this will result in significant consequences that can hurt your business.
Prioritise safety with regular testing and tagging
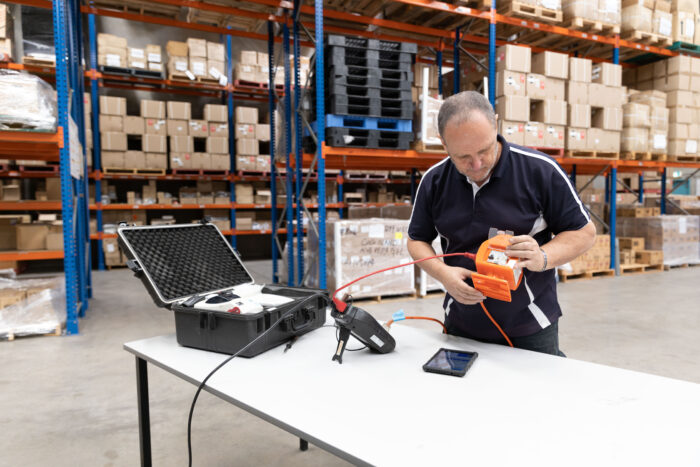
The frequency of testing and tagging will depend on the industry, equipment and regulations. Most of the guidelines are outlined in AS/NZS 3760:2022. Compliance with industry regulations should be one of the key priorities for any business to ensure smooth operations and minimise the chance of any issues. Precision Test and Tag is a Sydney testing and tagging company with years of experience.
Over the years, we have extended our expertise, refined our processes and adopted the latest technologies and trends to keep up with regulations and safety expectations. We remain committed to excellent customer service while ensuring your premises remain safe for customers and employees.
Our services include plug replacement, emergency light testing, RCD testing and more.
Contact Precision Test and Tag today for pricing information or to book your next testing service.