Australian Standards for Testing and Tagging
Electrical testing and tagging in NSW must be conducted in accordance with the relevant Australian standards. These standards outline the procedures for testing and tagging and the frequency of inspections based on the type of equipment and its usage. Industries may also follow the guidelines for test and tag colours based on testing months.
AS/NZS 3760
AS/NZS 3760:2010 specifies the testing intervals for different types of electrical equipment and the appropriate testing methods and records that need to be kept. It also outlines the qualifications and training required for testing and tagging professionals.
AS/NZS 3012
AS/NZS 3012 focuses on ensuring electrical safety practices during construction and demolition activities by setting out specific electrical installation and testing requirements.
AZ/NZS 2293
NSW businesses also need to comply with AS/NZS 2293 which outlines the requirements for emergency light testing. This standard applies to all commercial buildings, including office spaces, shopping centres, and industrial facilities.
AS 1851
AS 1851 covers the testing and tagging of fire extinguishers and fire equipment to ensure everything is in optimal working condition at all times, especially in case of a fire.
AS/NZS 60335.2.23
AS/NZS 60335.2.23 applies to the safety of electrical appliances in households and small businesses, including testing for microwaves, kettles, and hairdryers.
These standards provide guidelines for the frequency of testing and tagging and specific requirements for different types of equipment. It is important for businesses in NSW to stay up-to-date with any changes or updates to these standards to ensure compliance. Failing to comply with the appropriate Australian standards can result in penalties and fines.
How Often Should A Business Test and Tag Appliances?

The frequency of testing and tagging depends on the sector in which your business operates and is determined based on the type of appliance, usage, and the workplace environment. The cost of testing and tagging will also depend on the frequency and number of appliances to be tested.
High-risk Operating Environments
Industries like construction, demolition, and mining require more frequent testing and tagging due to their higher inherent hazards than less risky sectors. With these three sectors, testing and tagging portable electrical equipment is recommended every three months, and fixed and transportable equipment every six months.
Low-risk Operating Environments
In low-risk operating environments, such as offices, hotels and retail spaces, the recommended test and tag intervals are longer. For portable equipment, the interval can range from 12 months to 2 years depending on the type of industry. However, even in these low-risk environments, regular testing and tagging is still important to ensure safety and compliance.
What Happens If A Business Fails to Follow Test and Tag Regulations in NSW?
If a business fails to follow test and tag regulations in NSW, it can face consequences such as penalties and fines. This can result in safety, financial, and legal risks that businesses may want to avoid.
Employers should ideally take their responsibility seriously and ensure all workplace electrical equipment is regularly tested and maintained to keep employees and customers safe. Employers can prevent accidents and injuries by taking a proactive approach to workplace safety.
It is also important to note that all testing and tagging must be done by a competent person who has completed a recognised training course and has the necessary qualifications. This ensures that the testing is done correctly and effectively.
Choose A Reliable Test and Tag Company for Your Electrical Needs
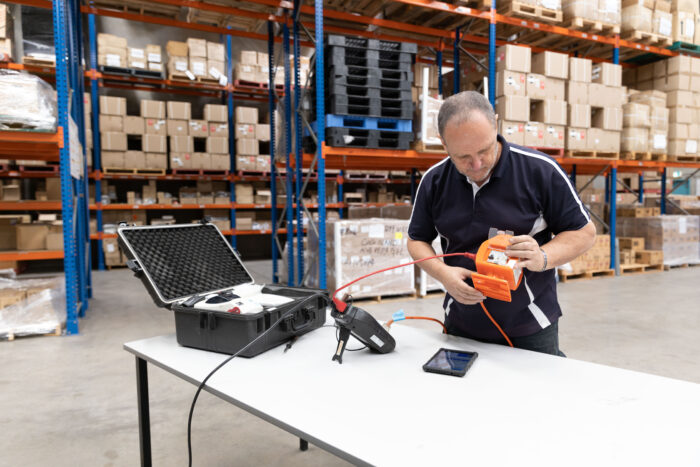
Electrical test and tag services are not just about meeting legal requirements. It is also a crucial part of risk management in the workplace. This helps prevent workplace accidents and injuries, protecting employees and the business. As safety is always a top priority, choose a reliable test and tag company in Sydney, like Precision Test and Tag, for all your electrical needs. Our experienced team can help you establish a regular testing and tagging schedule and keep records of all completed tests to ensure compliance with regulations.