Electrical testing and tagging is the process of checking electrical equipment for faults and safety issues and then attaching a tag to the equipment to indicate that it has been tested. The purpose is to reduce the risk of injuries or fatalities caused by electric shock or fire by identifying and removing any equipment that is not safe to use before anything happens.
The testing process involves two steps: visually inspecting the equipment for defects, damage, and missing components; and providing electrical tests measuring insulation resistance, polarity, and earth continuity.
Once the equipment has been tested, it is tagged with confirmation of the test results, including the test date, who performed it, and when the next test is due.
Types of electrical equipment needing testing
Testing and tagging of electrical appliances is compulsory in NSW. Electrical equipment in all office areas, workshops, factors and construction sites must be tested and tagged according to NSW SafeWork guidelines.
Electrical equipment can be classed into two categories – earthed appliances and double-insulated appliances. Earthed appliances include items like toasters and kettles while double insulated appliances consist of electrical tools.
Some types of electrical equipment require regular testing to identify faults. This will depend on the type of equipment and the environment. Some appliances that are regularly tested at workplaces include microwaves, computers, power tools, emergency lights, RCDs, electrical outlets, printers, photocopiers, fax machines, double-insulated appliances, leads, cord sets, wires and 3-phase devices.
Others include emergency light testing and fire extinguisher testing which require periodic test and tag checks. It’s important to keep in mind the frequency of testing and tagging to remain compliant with workplace safety guidelines.
Importance of testing and tagging at the workplace
Many accidents happen at the workplace due to faulty electrical equipment. For example, frayed cords, exposed wires and burnt terminals could all result in a preventable fire. Similarly, an appliance that’s not properly grounded could cause an electric shock, and a power tool with worn-out insulation could start a fire. For the safety of your employees and customers, it is important to carry out regular testing and tagging.
A professional test and tag service provider can assess risk and check all your equipment to ensure they are in good condition. Testing and tagging can help prevent accidents by identifying any electrical equipment that is not safe to use. This reduces the chances of someone being electrocuted or suffering long-term fire injuries.
Regular electrical testing and tagging inspections can help ensure the safety of your employees and your business. Apart from testing, it is also important to employ some additional safety measures:
- Educate employees about the risks and hazards posed by electricity.
- Encourage employees to report any damaged or faulty equipment
- Ensure all electrical equipment is properly maintained and stored
Industries that need testing and tagging
Some industries may have more testing and tagging guidelines than others depending on the nature of the workplace. According to SafeWork NSW guidelines for managing risks at the workplace, electrical equipment in higher-risk environments needs testing every 12 months. In some cases where electrical equipment is used for manufacturing, testing may be required every 12 months.
Some electrical equipment in industries like mining, demolition and construction may need testing and tagging more often due to the harsh nature of their work, which can damage electrical equipment faster. These industries must also follow guidelines for specific test and tag colours based on the testing months.
Businesses should not take testing and tagging lightly as they safeguard against electrical risks that could cause injury or death. Therefore, consulting with an experienced professional is important to protect your workplace.
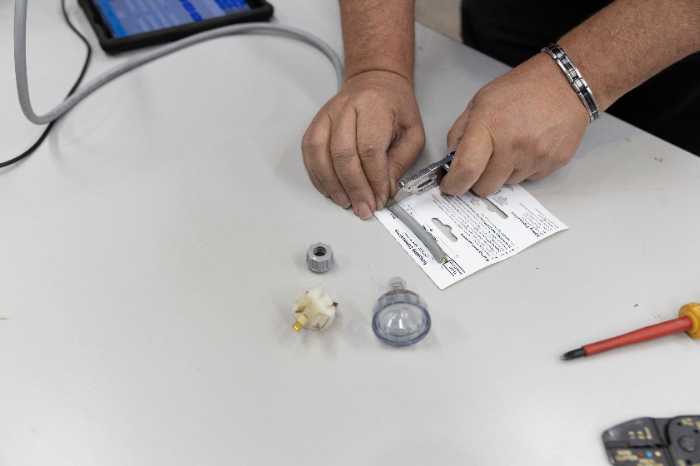
Who can perform testing and tagging?
A licensed professional who has completed the UEENEEP026A (Conduct In-Service Safety Testing) and UEENEEE101A (Apply Occupational Health and Safety Regulations) courses can perform electrical testing and tagging.
This means they have been trained to test and tag equipment in the workplace using competent electrical testing instruments and can interpret and record testing equipment results.
In addition to the requirements stated above, they must be able to demonstrate a good understanding of the tagging process and perform tests and visual inspections according to AS/NZS3760 standards to ensure the safety of all electrical appliances.
The bottom line is that anyone conducting testing and tagging must be fully qualified and capable of properly assessing the risks involved in each individual situation to reduce the risk of mishaps.
When should you test and tag your equipment?
Ideally, electrical equipment testing and tagging should be undertaken every 12 months according to SafeWork NSW test and tag guidelines.
Depending on the work environment and the risks posed by the electrical equipment, inspections and testing will occur at various intervals as indicated in the AS/NZS 3760. In normal offices, the expectation for testing and tagging electrical equipment is usually 12 months. In hostile environments like the construction industry, wiring and switchboards are inspected in 6-month intervals as indicated in the AS/NZS 3012. Fire extinguisher testing falls under AS 1851 and requires testing every six months.
The cost for testing and tagging will depend on the frequency and number of appliances being tested. With many different requirements, engaging a licensed professional trained to do the job right is important.
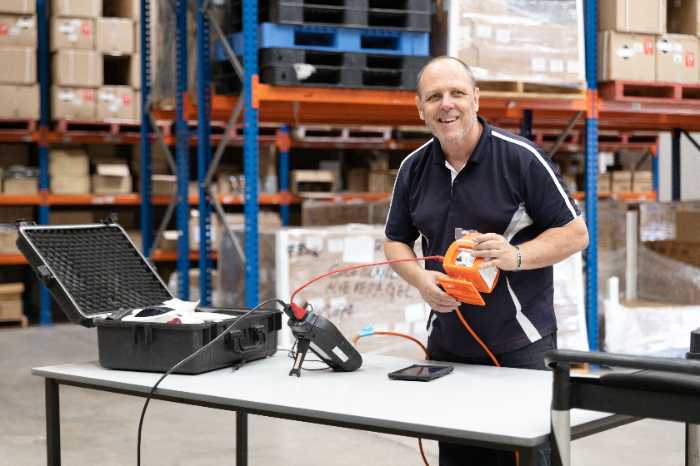
Final thoughts
Testing and tagging electrical equipment is an important measure that all businesses should undertake to ensure the safety of their employees and customers. While it may be required by law in some industries, even businesses in other sectors should consider implementing a risk management approach to testing and tagging.
Either way, you must have the means to carry this out properly. Avoid leaving everyone’s safety to chance by relying on the electrical test and tag specialists, Precision Test and Tag, for all your needs.
We offer specialised services like testing microwaves, power outlets, RCD testing, emergency lights, power tools, plug replacement, fire extinguisher testing etc. Keep up to date with the latest changes in electrical regulations so that you can be confident that your equipment is being tested and tagged using only the most current techniques.
Contact us today for more information about our testing and tagging services to keep your business safe.